SAP as an ERP system is more than just software; it’s a comprehensive solution transforming how businesses manage their resources. From finance and human resources to supply chain and customer relationship management, SAP integrates various departments into a single, unified platform. This allows for streamlined processes, improved efficiency, and better decision-making based on real-time data. But how does it actually work, and is it the right fit for every company?
Let’s explore the intricacies of this powerful system.
This article delves into the core functionalities of SAP ERP, examining its various modules and how they interact. We’ll explore the implementation process, highlighting both the benefits and challenges involved. We’ll also compare SAP to other major ERP systems and analyze its suitability for different industries and business sizes, providing a comprehensive overview of this crucial enterprise resource planning solution.
SAP ERP System Overview
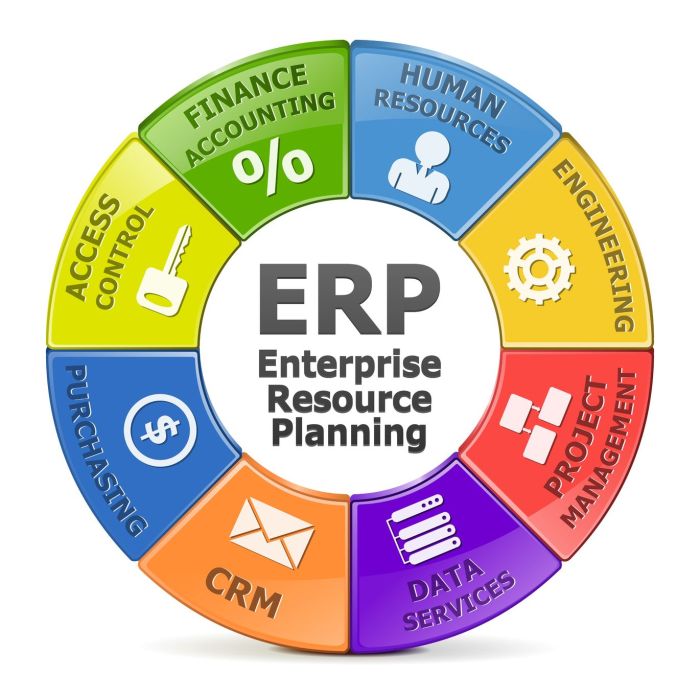
SAP, short for Systems, Applications & Products in Data Processing, is a leading Enterprise Resource Planning (ERP) system. It’s essentially a comprehensive software suite designed to integrate all facets of a business’s operations, from planning and purchasing to manufacturing, sales, and finance. Think of it as a central nervous system for a company, allowing for efficient data flow and informed decision-making.SAP ERP’s core functionalities revolve around streamlining business processes and providing a single source of truth for critical data.
This involves managing various aspects of a business, including financial accounting, materials management, human resources, and sales and distribution. A well-implemented SAP system can significantly improve efficiency, reduce costs, and enhance overall business performance.
SAP ERP Modules and Their Interrelationships
The power of SAP lies in its modularity. Different modules cater to specific business needs, but they are designed to seamlessly interact, sharing data and creating a holistic view of the organization. For example, data from the Sales and Distribution module (SD) directly feeds into the Financial Accounting module (FI), providing real-time insights into revenue and profitability. Similarly, the Production Planning module (PP) interacts with Materials Management (MM) to ensure that the necessary materials are available for production.
This interconnectedness is crucial for efficient operations and informed decision-making. Key modules include:
- Financial Accounting (FI): Manages financial transactions, general ledger, accounts payable, and accounts receivable.
- Materials Management (MM): Oversees procurement, inventory management, and warehouse operations.
- Sales and Distribution (SD): Handles order processing, delivery, billing, and customer relationship management (CRM) aspects.
- Production Planning (PP): Plans and manages the manufacturing process, including capacity planning and materials requirements planning (MRP).
- Human Capital Management (HCM): Manages employee data, payroll, benefits, and talent management.
These are just some of the core modules; SAP offers a wide range of additional modules to cater to specialized industry needs. The interrelationship between these modules ensures a unified and efficient flow of information throughout the organization. For instance, accurate inventory data from MM is crucial for effective production planning in PP, and timely sales data from SD is essential for accurate financial reporting in FI.
Comparison of SAP ERP with Other Major ERP Systems
Choosing the right ERP system is a critical decision for any business. Here’s a comparison of SAP ERP with some key competitors:
System Name | Key Features | Target Market | Strengths |
---|---|---|---|
SAP ERP | Comprehensive functionality, strong integration, robust reporting, high scalability | Large enterprises, multinational corporations | Industry-leading functionality, extensive customization options, global reach |
Oracle ERP | Integrated suite of applications, strong financial management capabilities, robust security | Large enterprises, diverse industries | Powerful financial management tools, high security, scalability |
Microsoft Dynamics 365 | Cloud-based solution, user-friendly interface, good integration with Microsoft Office 365 | Small to medium-sized businesses (SMBs), specific industry solutions | Ease of use, cloud-based accessibility, cost-effectiveness for SMBs |
SAP ERP Implementation Process
Implementing SAP ERP is a monumental undertaking, akin to building a skyscraper from the ground up. It requires meticulous planning, significant resources, and a dedicated team to navigate the complex process successfully. Understanding the phases, challenges, and best practices is crucial for a smooth and efficient deployment.
The SAP ERP implementation process is a multifaceted journey, typically divided into distinct phases, each with its own set of tasks and objectives. A well-defined approach ensures a streamlined transition and minimizes disruption to business operations.
Phases of SAP ERP Implementation
A typical SAP ERP implementation project unfolds in several key phases. These phases are iterative and often overlap, requiring constant communication and collaboration among stakeholders.
- Project Initiation and Planning: This initial phase involves defining project scope, objectives, and timelines. Key activities include forming a project team, securing budget approval, and conducting a thorough assessment of the organization’s current business processes.
- Blueprinting and Design: This crucial phase focuses on designing the future state of the SAP system. It involves mapping existing business processes to SAP functionalities, customizing the system to meet specific organizational needs, and defining data migration strategies.
- Realization: This phase involves the actual configuration and development of the SAP system. Developers customize the system based on the blueprint, data migration is performed, and interfaces with other systems are established. Testing is a crucial element of this phase.
- Testing: Rigorous testing is critical to ensure the system functions correctly and meets business requirements. This phase involves unit testing, integration testing, user acceptance testing (UAT), and performance testing.
- Go-Live and Post-Implementation Support: This final phase marks the transition to the new SAP system. Post-implementation support is essential to address any issues that arise and provide ongoing training and maintenance.
Challenges in SAP ERP Implementation
Despite careful planning, SAP ERP implementations often face significant challenges. These challenges can impact timelines, budgets, and ultimately, the success of the project.
- Data Migration: Migrating large volumes of data from legacy systems to SAP can be complex and time-consuming, potentially leading to data loss or inconsistencies.
- Integration with Existing Systems: Integrating SAP with existing systems requires careful planning and execution to ensure seamless data flow and avoid disruptions.
- Change Management: Successfully implementing SAP requires buy-in from all stakeholders. Resistance to change, lack of training, and insufficient communication can derail the project.
- Project Scope Creep: Uncontrolled expansion of project scope can lead to cost overruns and delays. Clear definition and management of scope are crucial.
- Resource Constraints: SAP implementations require skilled resources, both internal and external. Shortages of qualified personnel can impact project timelines and quality.
Best Practices for Successful SAP ERP Deployment
Several best practices can significantly increase the likelihood of a successful SAP ERP implementation. These practices focus on proactive planning, effective communication, and continuous monitoring.
- Clearly Defined Scope and Objectives: Establish a clear understanding of the project goals, scope, and deliverables from the outset.
- Strong Project Management: Employ experienced project managers to oversee all aspects of the implementation.
- Comprehensive User Training: Provide thorough training to all users to ensure they are comfortable using the new system.
- Effective Communication: Maintain open and consistent communication among all stakeholders throughout the project lifecycle.
- Iterative Approach: Adopt an iterative approach, allowing for flexibility and adjustments as the project progresses.
SAP ERP Implementation Flowchart
A visual representation of the key steps can simplify the understanding of the process. The following describes a simplified flowchart:
Imagine a flowchart starting with a “Start” oval. This flows into a rectangle labeled “Project Initiation & Planning.” From there, an arrow leads to a rectangle labeled “Blueprinting & Design.” Another arrow leads to a rectangle labeled “Realization,” followed by a rectangle labeled “Testing.” Finally, an arrow leads from “Testing” to a rectangle labeled “Go-Live & Post-Implementation Support,” concluding with an “End” oval.
Each rectangle represents a phase with internal processes and decision points not explicitly shown for brevity.
Benefits and Drawbacks of Using SAP ERP
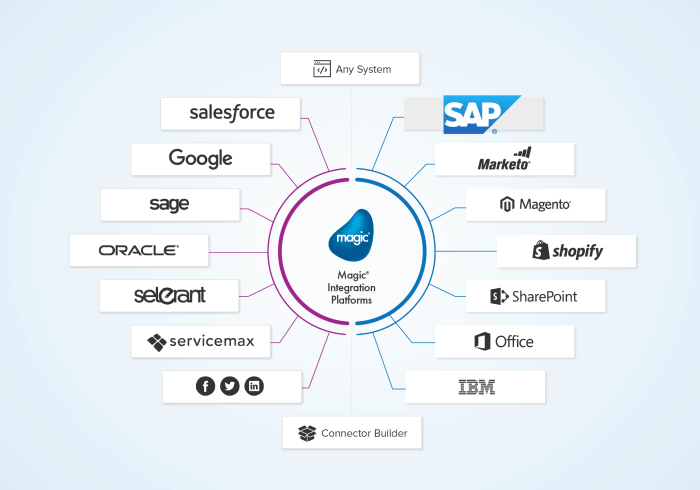
So, you’re thinking about implementing SAP ERP? It’s a big decision, one that could revolutionize your business processes or, if not handled correctly, become a massive headache. Let’s break down the pros and cons to help you make an informed choice. This isn’t about hype; it’s about the cold, hard facts.
SAP ERP, while a powerful tool, isn’t a magic bullet. Its effectiveness depends heavily on proper implementation, ongoing maintenance, and a clear understanding of your business needs. Ignoring these factors can quickly turn a potential advantage into a significant disadvantage. This section dives deep into the practical benefits and drawbacks, offering a realistic perspective to help you decide if SAP ERP is the right fit for your organization.
Advantages of Using SAP ERP
The benefits of SAP ERP are numerous and span various aspects of business operations. From streamlined processes to improved decision-making, the potential ROI can be substantial, especially for larger enterprises. However, even smaller businesses can find value in specific modules tailored to their needs.
- Improved Efficiency and Productivity: SAP ERP automates many manual processes, freeing up employees to focus on more strategic tasks. Imagine the time saved by automating invoice processing or inventory management – that’s directly translated into increased productivity and reduced operational costs.
- Enhanced Data Visibility and Reporting: SAP’s centralized database provides a single source of truth, giving businesses a 360-degree view of their operations. This real-time data allows for better informed decision-making, identifying trends and potential issues proactively.
- Better Collaboration and Communication: Different departments can access and share the same information, improving collaboration and reducing communication silos. This integrated approach streamlines workflows and eliminates duplicated efforts.
- Scalability and Flexibility: SAP ERP systems can adapt to the changing needs of a business, whether it’s expanding into new markets or integrating new technologies. This scalability makes it a worthwhile investment for businesses anticipating growth.
- Improved Compliance and Risk Management: SAP ERP helps businesses meet regulatory requirements and manage risks more effectively. Features like built-in audit trails and security controls enhance compliance and protect sensitive data.
Disadvantages of Using SAP ERP
Despite the significant advantages, SAP ERP isn’t without its drawbacks. These challenges often stem from the complexity of the system and the significant investment required.
- High Implementation Costs: The initial investment in software licenses, consulting services, customization, and training can be substantial, especially for large-scale implementations. This cost needs careful consideration and budgeting.
- Complexity and Steep Learning Curve: SAP ERP is a complex system, requiring specialized skills and training for users. This can lead to increased training costs and a longer period before employees become fully proficient.
- Customization Challenges: While SAP offers a highly customizable platform, extensive modifications can increase costs and complexity, potentially leading to integration issues and delays.
- Vendor Lock-in: Migrating away from SAP ERP can be a costly and time-consuming process, potentially creating vendor lock-in.
- Ongoing Maintenance Costs: Maintaining and updating the system requires ongoing investment in software licenses, support contracts, and technical expertise.
Total Cost of Ownership (TCO) Comparison
The TCO of SAP ERP is significantly higher than many alternative ERP solutions. However, this needs to be weighed against the potential return on investment (ROI). Smaller businesses might find that cloud-based alternatives or open-source options offer a more cost-effective solution, while larger enterprises with complex needs might find the investment in SAP justified by the enhanced efficiency and scalability.
A direct TCO comparison is difficult without specifics about the business size, industry, and desired functionalities. However, a general rule of thumb is that SAP’s TCO will be higher upfront and potentially over the long term compared to solutions like Microsoft Dynamics 365 or Odoo, but potentially lower in the long run than building a bespoke solution. The choice depends on a thorough cost-benefit analysis tailored to the specific business context.
Specific SAP ERP Modules and their Uses
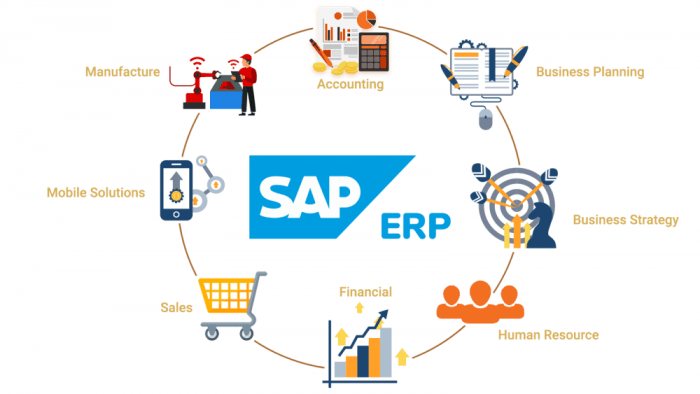
SAP ERP’s power lies in its modularity. Different businesses require different functionalities, and SAP allows for a tailored approach. Understanding the core modules is key to grasping the system’s potential and its adaptability across diverse industries. This section dives into some of the most crucial modules, highlighting their individual strengths and practical applications.
SAP Financial Accounting (FI) Module
The SAP FI module forms the backbone of any SAP ERP implementation. It manages a company’s financial transactions, providing a centralized system for recording, processing, and reporting financial data. This includes general ledger accounting, accounts receivable (AR), accounts payable (AP), asset accounting, and bank accounting. The module ensures compliance with accounting standards and provides real-time insights into the financial health of the organization.
Think of it as the central nervous system of a company’s financial operations, connecting all the financial dots. Data from other modules feeds into FI, creating a holistic financial picture. For example, sales data from the SD module directly impacts accounts receivable in FI.
SAP Controlling (CO) Module
While FI focuses on external financial reporting, CO is geared towards internal management accounting. It provides tools for cost accounting, profitability analysis, and performance management. CO allows businesses to track costs associated with specific projects, products, or departments, enabling better decision-making and resource allocation. Imagine a manufacturing company using CO to analyze the cost of producing each product line, identifying areas for improvement and optimizing production processes.
This module is invaluable for internal control and strategic planning. Key functionalities include cost center accounting, profit center accounting, and activity-based costing.
SAP Materials Management (MM) Module
Efficient inventory management is crucial for any business, and the SAP MM module is designed to streamline this process. It manages the entire lifecycle of materials, from procurement to storage and consumption. This includes purchasing, inventory control, warehouse management, and vendor management. Features like automated purchase order generation, inventory tracking, and demand forecasting ensure optimal stock levels, reducing storage costs and preventing stockouts.
For instance, a retail company can leverage MM to accurately predict demand for seasonal items, ensuring sufficient stock without overstocking.
SAP, a leading name in Enterprise Resource Planning (ERP) systems, offers comprehensive solutions for businesses of all sizes. Want to explore other powerful options? Check out this list of top erp systems to see how SAP stacks up against the competition. Ultimately, the best ERP system depends on your specific needs, but SAP remains a major player in the field.
SAP Sales and Distribution (SD) Module
The SD module manages the entire sales process, from order creation to delivery and billing. It integrates with other modules, such as MM (for inventory checks) and FI (for invoicing). Businesses use SD to manage customer orders, track sales performance, and streamline the order-to-cash cycle. A clothing retailer, for example, could use SD to manage online and in-store sales, track customer preferences, and generate sales reports.
This module is crucial for sales forecasting, pricing strategies, and overall revenue management. Features like order management, pricing, delivery scheduling, and billing are all handled within the SD module.
SAP ERP and Industry-Specific Solutions
SAP ERP’s strength lies not just in its comprehensive functionality, but also in its remarkable adaptability across diverse industries. Unlike a one-size-fits-all approach, SAP tailors its solutions to meet the unique operational needs and challenges of various sectors, resulting in significantly improved efficiency and profitability. This adaptability is achieved through a combination of pre-built industry-specific solutions and robust customization options.SAP’s industry-specific solutions leverage the core ERP functionality while incorporating specialized modules and functionalities relevant to particular industries.
This approach ensures that businesses can benefit from a pre-configured system that addresses their key requirements, reducing implementation time and costs. The solutions are not merely superficial add-ons; they reflect a deep understanding of the intricacies and best practices within each industry.
Industry-Specific Solutions Built on SAP ERP
SAP offers a wide array of industry-specific solutions built on its ERP platform. These solutions are not simply generic ERP systems with a few industry-specific features bolted on; they are deeply integrated and designed to streamline processes unique to each sector. For example, in manufacturing, solutions focus on optimizing production planning, supply chain management, and quality control. In retail, the focus shifts to inventory management, point-of-sale systems, and customer relationship management.
Healthcare solutions prioritize patient management, billing, and regulatory compliance. This tailored approach ensures that the system is not just functional, but also intuitive and efficient for users within each industry.
Customization Options within SAP ERP
Beyond pre-built industry solutions, SAP ERP offers extensive customization options to cater to the specific needs of individual businesses within each vertical. This allows companies to adapt the system to their unique workflows, reporting requirements, and business processes. Customization can range from minor adjustments to the user interface to the development of entirely new modules or functionalities. Experienced SAP consultants play a vital role in guiding businesses through the customization process, ensuring that changes are implemented effectively and efficiently, without compromising the integrity of the core system.
This flexibility is a key factor in SAP’s enduring success and widespread adoption across a multitude of industries.
Examples of SAP ERP Industry Solutions and their Key Features
Industry | Solution Name | Key Features | Benefits |
---|---|---|---|
Manufacturing | SAP Manufacturing Execution (SAP ME) | Production planning and scheduling, shop floor control, quality management, maintenance management | Improved production efficiency, reduced downtime, enhanced product quality |
Retail | SAP Retail | Point-of-sale (POS) management, merchandise planning, supply chain management, customer relationship management (CRM) | Improved sales performance, optimized inventory levels, enhanced customer loyalty |
Healthcare | SAP for Healthcare | Patient management, billing and claims processing, regulatory compliance, clinical documentation | Improved patient care, streamlined administrative processes, enhanced revenue cycle management |
Financial Services | SAP for Banking | Core banking processes, risk management, regulatory compliance, customer relationship management | Improved operational efficiency, reduced risk, enhanced customer satisfaction |
Future Trends in SAP ERP
SAP ERP, while a robust and established system, isn’t static. It’s constantly evolving to meet the demands of a rapidly changing business landscape, driven by technological advancements and shifting market needs. The future of SAP ERP is inextricably linked to the adoption of cutting-edge technologies and its ability to adapt to the increasing digitalization of businesses worldwide.The integration of cloud computing, artificial intelligence, and blockchain technology is reshaping the capabilities and accessibility of SAP ERP, leading to increased efficiency, improved decision-making, and enhanced overall business performance.
This evolution is not just about technological upgrades; it’s about creating a more agile, responsive, and intelligent enterprise.
Cloud Computing’s Impact on SAP ERP
The shift towards cloud-based SAP solutions is undeniable. Cloud deployment offers significant advantages, including reduced upfront investment costs, scalability to accommodate fluctuating business demands, enhanced accessibility through remote access, and simplified maintenance and updates. SAP S/4HANA Cloud, for example, represents a significant step towards this cloud-first strategy, providing a comprehensive suite of ERP functionalities accessible through a subscription model.
Companies like Netflix, leveraging cloud-based solutions for their vast operational needs, demonstrate the scalability and adaptability offered by this approach. This allows businesses to focus on core competencies rather than IT infrastructure management.
Emerging Trends: AI, Machine Learning, and Blockchain
Artificial intelligence (AI) and machine learning (ML) are transforming how SAP ERP systems operate. AI-powered functionalities can automate routine tasks, analyze vast datasets to identify patterns and predict future trends, and provide real-time insights for improved decision-making. Imagine an AI-powered system predicting potential supply chain disruptions based on real-time data analysis, allowing for proactive mitigation strategies. Similarly, machine learning algorithms can optimize production processes, leading to cost savings and increased efficiency.
Blockchain technology offers enhanced security and transparency, particularly useful in supply chain management by providing immutable records of transactions and improving traceability. Companies in the pharmaceutical industry, for example, are exploring blockchain to ensure drug authenticity and combat counterfeiting.
SAP ERP’s Adaptation to the Changing Business Landscape
SAP ERP is continuously adapting to accommodate evolving business needs and industry-specific requirements. This includes integrating with emerging technologies, enhancing user experience through intuitive interfaces, and offering specialized solutions for various industries. For instance, the integration of Internet of Things (IoT) data into SAP ERP systems allows for real-time monitoring of assets and processes, leading to improved operational efficiency.
This adaptability ensures that SAP ERP remains a relevant and valuable tool for businesses of all sizes and across all sectors.
The Future of SAP ERP and its Role in Digital Transformation
The future of SAP ERP is intertwined with the broader digital transformation journey of businesses. SAP ERP systems will increasingly become the central nervous system of the intelligent enterprise, integrating various data sources, automating processes, and providing real-time insights to support strategic decision-making. This will involve further integration with cloud platforms, AI and ML capabilities, and other emerging technologies to create a truly holistic and intelligent business ecosystem.
The ability to leverage data effectively will be key, enabling companies to personalize customer experiences, optimize operations, and achieve significant competitive advantages. Forward-thinking companies are already investing in these advancements, positioning themselves for future success in the rapidly evolving digital economy.
Illustrative Example: A Manufacturing Company Using SAP ERP: Sap As An Erp System
Let’s imagine “GearGrind,” a mid-sized manufacturer of precision gears for the automotive industry. GearGrind faces the typical challenges of managing a complex supply chain, including procurement, production planning, inventory control, and sales order fulfillment. Implementing SAP ERP helps streamline these processes and improve overall efficiency.GearGrind utilizes several core SAP modules to manage its operations. The integration between these modules allows for real-time data flow and informed decision-making across the entire organization.
Supply Chain Management with SAP PP and MM Modules
GearGrind leverages SAP’s Production Planning (PP) and Materials Management (MM) modules extensively. The PP module helps plan production schedules based on sales forecasts and available resources. Simultaneously, the MM module manages procurement, ensuring timely delivery of raw materials and components. For example, when a sales order for a specific gear type is received, the system automatically triggers a materials requirement planning (MRP) run within the PP module.
This MRP run analyzes the bill of materials (BOM) for that gear, determining the necessary raw materials and components. The system then automatically creates purchase requisitions in the MM module for any missing materials, triggering the procurement process.
Inventory Management with SAP WM and Inventory Management
Once raw materials arrive, they are registered in the warehouse management (WM) module. SAP WM provides real-time visibility into inventory levels, location, and status. This real-time tracking minimizes storage costs and prevents stockouts. The integration with the MM module ensures that inventory data is consistently updated, providing an accurate picture of available resources for production. This also allows for efficient inventory control, preventing overstocking or shortages of crucial components.
Sales Order Fulfillment and Financial Management with SAP SD and FI Modules, Sap as an erp system
When production is complete, the finished goods are moved to the warehouse, updated in WM, and become available for shipment. The sales and distribution (SD) module manages the sales order process, from order entry to delivery. The SD module interacts with the PP module to ensure that orders are fulfilled on time. Upon shipment, the financial accounting (FI) module automatically generates accounting entries, reflecting the revenue and cost of goods sold.
This seamless integration ensures accurate financial reporting and simplifies reconciliation processes.
Step-by-Step Process Flow
- Sales Order Received: A customer places an order via the SD module.
- MRP Run Triggered: The system automatically triggers an MRP run in the PP module based on the sales order and BOM.
- Purchase Requisitions Generated: The MM module automatically generates purchase requisitions for any missing materials.
- Procurement Process: The procurement process is initiated, tracking the materials from ordering to receipt.
- Production Scheduling: The PP module schedules production based on available resources and material availability.
- Production Execution: Production is executed, and the system tracks progress and resource consumption.
- Goods Receipt: Finished goods are moved to the warehouse and registered in the WM module.
- Delivery and Billing: The SD module manages the delivery and billing process.
- Financial Accounting: The FI module automatically updates the financial records.
Integration Between SAP Modules
The seamless integration between SAP’s various modules is key to GearGrind’s success. For instance, the data flow between the PP, MM, WM, SD, and FI modules ensures accurate inventory tracking, efficient production planning, timely order fulfillment, and accurate financial reporting. This integrated approach eliminates data silos and provides a single source of truth for all business processes. This reduces errors, improves decision-making, and ultimately boosts efficiency and profitability.