Manufacturing software is revolutionizing industries, streamlining processes from design to delivery. This isn’t just about spreadsheets and scheduling anymore; we’re talking intelligent systems leveraging AI, IoT, and data analytics to boost efficiency, slash costs, and build a more sustainable future. This deep dive explores the various types of manufacturing software, their key features, implementation strategies, and the exciting trends shaping their future.
From Enterprise Resource Planning (ERP) systems managing entire operations to Manufacturing Execution Systems (MES) optimizing production lines, the software landscape is diverse and powerful. Understanding these tools and their integration is crucial for any manufacturer aiming for a competitive edge in today’s dynamic market. We’ll break down the complexities, explore real-world examples, and highlight the transformative impact of these technologies on modern manufacturing.
Types of Manufacturing Software
The modern manufacturing landscape relies heavily on sophisticated software solutions to optimize processes, improve efficiency, and enhance overall productivity. From design to delivery, various software categories play crucial roles, each with unique functionalities and applications. Understanding these categories is key to selecting the right tools for a manufacturing business of any size.
Manufacturing software can be broadly categorized into several key types, each designed to address specific aspects of the manufacturing process. These categories often overlap and integrate with one another to create a comprehensive and efficient system. Let’s delve into the most prominent categories and explore some examples.
Enterprise Resource Planning (ERP) Software, Manufacturing software
ERP systems integrate various business functions into a unified system. This includes planning, purchasing, inventory management, sales, marketing, and human resources. In manufacturing, ERP software helps manage the entire production lifecycle, from raw materials procurement to finished goods delivery. This integrated approach streamlines operations, reduces data silos, and provides a holistic view of the business.
Examples of popular ERP systems include SAP S/4HANA, Oracle NetSuite, and Microsoft Dynamics 365. SAP S/4HANA, for instance, offers advanced analytics and real-time insights into manufacturing processes, enabling better decision-making. Oracle NetSuite provides a comprehensive suite of tools for managing various aspects of the business, including manufacturing-specific modules. Microsoft Dynamics 365 offers flexible deployment options and integrates well with other Microsoft products.
These ERP systems typically offer cloud-based, on-premise, and hybrid deployment models, allowing businesses to choose the option that best suits their infrastructure and needs. Cloud-based deployments offer scalability and accessibility, while on-premise solutions provide greater control over data security. Hybrid models combine the benefits of both approaches.
Manufacturing Execution Systems (MES) Software
MES software focuses specifically on the shop floor, providing real-time visibility into production processes. It monitors equipment performance, tracks materials, manages labor, and collects data to optimize production efficiency. MES systems are crucial for improving production scheduling, reducing downtime, and enhancing product quality.
Examples of MES software include Rockwell Automation’s FactoryTalk MES, Siemens Opcenter Execution, and GE Digital’s Predix. Rockwell Automation’s FactoryTalk MES integrates seamlessly with other Rockwell automation products, providing a comprehensive automation solution. Siemens Opcenter Execution offers advanced analytics and reporting capabilities, enabling data-driven decision-making. GE Digital’s Predix (now part of GE’s broader industrial internet platform) focuses on connecting various industrial assets and leveraging data for improved operational efficiency.
Deployment models for MES software mirror those of ERP systems, with cloud-based, on-premise, and hybrid options available. The choice depends on factors like existing infrastructure, security requirements, and budget.
Computer-Aided Design/Computer-Aided Manufacturing (CAD/CAM) Software
CAD/CAM software is used for designing and manufacturing products. CAD software allows engineers and designers to create 3D models of products, while CAM software translates these designs into instructions for manufacturing equipment. This integration streamlines the design-to-manufacturing process, reducing errors and improving efficiency.
Examples include Autodesk Inventor, SolidWorks, and Mastercam. Autodesk Inventor offers a comprehensive suite of tools for 3D modeling, simulation, and documentation. SolidWorks is known for its user-friendly interface and extensive library of tools. Mastercam is a widely used CAM software that supports a wide range of CNC machines.
CAD/CAM software is typically deployed on-premise, though cloud-based options are emerging, particularly for collaborative design and access to powerful processing capabilities. Hybrid models are also possible, with some components running on-premise and others in the cloud.
Product Lifecycle Management (PLM) Software
PLM software manages the entire lifecycle of a product, from initial concept to end-of-life. This includes design, manufacturing, marketing, sales, and service. PLM systems help companies manage product data, collaborate with suppliers, and track product performance.
Examples include Siemens Teamcenter, Dassault Systèmes 3DEXPERIENCE Platform, and PTC Windchill. Siemens Teamcenter offers a comprehensive platform for managing product data and collaborating with stakeholders throughout the product lifecycle. Dassault Systèmes’ 3DEXPERIENCE Platform is a cloud-based platform that provides a collaborative environment for product development. PTC Windchill provides a robust PLM solution with strong integration capabilities.
PLM software is increasingly offered as cloud-based solutions, although on-premise and hybrid deployments remain common. The choice often depends on the size and complexity of the organization and its security needs.
Comparison of Three Prominent Solutions
Feature | SAP S/4HANA | Siemens Opcenter Execution | Autodesk Inventor |
---|---|---|---|
Focus | Enterprise Resource Planning | Manufacturing Execution | CAD/CAM |
Key Functionalities | Integrated business processes, financial management, supply chain management | Real-time shop floor monitoring, production optimization, quality control | 3D modeling, simulation, design automation |
Deployment Models | Cloud, On-Premise, Hybrid | Cloud, On-Premise, Hybrid | Primarily On-Premise, Cloud options emerging |
Key Features and Functionalities
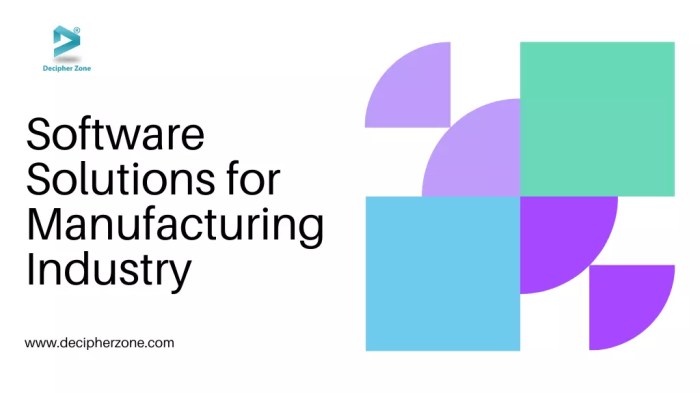
Manufacturing software is the backbone of efficient and profitable production. These sophisticated systems streamline operations, improve decision-making, and ultimately boost the bottom line. Understanding their core functionalities is crucial for any manufacturer looking to modernize their processes.Modern manufacturing software packages share several key functionalities. These features, often integrated within a single platform or through seamless interoperability, contribute to a holistic view of the manufacturing process, enabling better control and optimization.
Core Functionalities of Manufacturing Software
Most manufacturing software packages include core functionalities such as planning and scheduling, inventory management, quality control, and production tracking. Planning and scheduling modules help optimize resource allocation and production timelines, minimizing delays and maximizing efficiency. Inventory management systems provide real-time visibility into stock levels, reducing waste from overstocking or production halts due to shortages. Quality control features ensure adherence to standards, minimizing defects and improving product quality.
Production tracking capabilities offer insights into production performance, allowing for identification of bottlenecks and areas for improvement. These are essential building blocks for a streamlined and data-driven manufacturing environment.
Benefits of Integrating Different Manufacturing Software Systems
The benefits of integrating various manufacturing software systems are significant. Integration eliminates data silos, fostering a unified view of operations across different departments and processes. For example, integrating Enterprise Resource Planning (ERP) software with a Manufacturing Execution System (MES) enables seamless data flow between planning, execution, and reporting. This integrated approach facilitates real-time visibility into production, inventory, and order fulfillment, improving responsiveness to customer demands and market changes.
Data inconsistencies and manual data entry are minimized, saving time and reducing the risk of errors. Ultimately, integrated systems lead to improved efficiency, reduced costs, and enhanced decision-making capabilities.
Manufacturing software relies heavily on data analysis to optimize production and predict market trends. Understanding key performance indicators (KPIs) is crucial, and that’s where insights from business iintelligence segments become invaluable. By integrating these segments, manufacturers gain a clearer picture, enabling better decision-making for their software and overall operations.
The Role of Data Analytics and Reporting in Modern Manufacturing Software
Data analytics and reporting are crucial components of modern manufacturing software. These capabilities transform raw production data into actionable insights, empowering manufacturers to identify trends, optimize processes, and improve overall performance. For example, advanced analytics can pinpoint production bottlenecks, predict equipment failures, and optimize inventory levels. Comprehensive reporting features allow manufacturers to track key performance indicators (KPIs) such as production output, defect rates, and on-time delivery.
This data-driven approach fosters continuous improvement and supports informed decision-making at all levels of the organization. The ability to visualize data through dashboards and reports provides a clear picture of operational performance, making it easier to identify areas needing attention.
Hypothetical Manufacturing Process Optimization
Let’s consider a hypothetical furniture manufacturing process and illustrate how software can optimize it. Imagine a company producing custom-made wooden chairs. The process involves design, cutting, assembly, finishing, and packaging. By implementing appropriate software solutions, significant improvements can be achieved.
Step | Software Tools Used | Data Collected | Resulting Improvements |
---|---|---|---|
Design & Order Management | CAD software, CRM | Customer specifications, material requirements, production timelines | Reduced design errors, improved order accuracy, faster order processing |
Cutting & Material Handling | CAM software, Inventory Management System | Material usage, cutting times, waste levels | Optimized material usage, reduced waste, improved cutting efficiency |
Assembly | MES, Production Tracking System | Assembly times, defect rates, labor costs | Improved assembly speed, reduced defects, better labor cost control |
Finishing & Packaging | Quality Control System, Warehouse Management System | Finishing times, defect rates, packaging efficiency | Improved product quality, faster packaging, reduced shipping errors |
Implementation and Integration
Successfully implementing manufacturing software is crucial for maximizing its benefits. A smooth transition requires careful planning, robust testing, and a clear understanding of potential integration challenges, particularly with existing legacy systems. Ignoring these aspects can lead to costly delays, operational disruptions, and ultimately, a failed implementation.
Implementing and integrating manufacturing software involves a multifaceted approach. It’s not just about installing the software; it’s about transforming how your manufacturing processes operate. This requires a comprehensive strategy that addresses everything from data migration to employee training. Let’s explore best practices and common hurdles.
Best Practices for Implementing Manufacturing Software
Implementing manufacturing software effectively requires a structured approach. Ignoring best practices can lead to significant setbacks. Following these guidelines increases the likelihood of a successful and efficient implementation.
- Thorough Needs Assessment: Before selecting any software, conduct a detailed analysis of your current manufacturing processes, identifying areas for improvement and the specific functionalities needed. This involves understanding your production workflow, data requirements, and reporting needs.
- Vendor Selection and Due Diligence: Carefully evaluate potential vendors, comparing their software features, pricing, implementation support, and customer reviews. Request demos and references to ensure the software aligns with your needs and the vendor is reliable.
- Phased Implementation: Implement the software in phases, starting with a pilot project in a specific area of your manufacturing operation. This allows for testing and refinement before a full-scale rollout, minimizing disruption and risk.
- Comprehensive Training: Provide comprehensive training to all employees who will be using the software. This ensures user adoption and minimizes errors. Training should cover all aspects of the software, including data entry, reporting, and troubleshooting.
- Change Management: Implement a change management plan to address employee concerns and facilitate a smooth transition. This includes clear communication, ongoing support, and addressing any resistance to adopting new technology.
Challenges of Integrating Legacy Systems
Integrating legacy systems with new manufacturing software can present significant challenges. The incompatibility of data formats and structures, along with the potential for data loss, are common concerns. Careful planning and the right approach are essential.
- Data Migration Issues: Legacy systems often use different data formats and structures than modern software. Migrating data requires careful planning and the use of appropriate data migration tools to ensure data accuracy and integrity.
- System Compatibility: Ensuring compatibility between legacy systems and new software requires careful evaluation of interfaces and APIs. Custom integrations may be necessary, adding to the cost and complexity of the implementation.
- Data Cleansing and Transformation: Before migration, legacy data often needs cleaning and transformation to ensure its compatibility with the new system. This process can be time-consuming and resource-intensive.
Step-by-Step Guide for System Migration
Migrating from an older system to a newer solution requires a well-defined plan. A phased approach minimizes disruption and maximizes the chances of a successful transition.
- Planning and Assessment: Define project goals, scope, and timeline. Assess current system capabilities and identify areas for improvement. This phase also includes selecting the new software and vendor.
- Data Migration Strategy: Develop a detailed plan for migrating data from the old system to the new one. This includes data cleansing, transformation, and validation.
- System Configuration and Testing: Configure the new software to meet your specific requirements. Conduct thorough testing to identify and resolve any issues before go-live.
- Training and User Acceptance Testing (UAT): Train employees on the new system and conduct UAT to ensure the system meets user needs and expectations.
- Go-Live and Post-Implementation Support: Implement the new system and provide ongoing support to users. Monitor system performance and address any issues that arise.
Implementation Process Flowchart
A visual representation of the implementation process helps illustrate the stages and dependencies. This flowchart depicts a typical implementation process, though specific steps might vary based on the complexity of the project and the software chosen.
Imagine a flowchart with the following boxes connected by arrows, representing a sequential process:
1. Planning & Assessment: This box encompasses needs analysis, vendor selection, and project scoping.
2. System Design & Configuration: This box details the setup and customization of the new software.
3. Data Migration: This box covers data extraction, transformation, loading, and validation.
4. System Testing (Unit, Integration, User Acceptance): This box represents the different levels of testing performed to ensure functionality and user satisfaction.
5. Training & Deployment: This box includes user training and the actual launch of the new system.
6. Post-Implementation Support & Monitoring: This box involves ongoing support, system monitoring, and performance evaluation.
Impact on Manufacturing Processes: Manufacturing Software
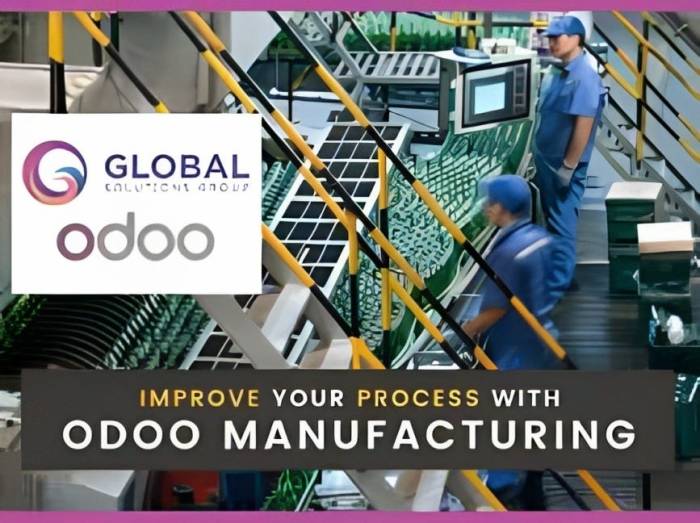
Manufacturing software has revolutionized how goods are produced, impacting every stage from initial design to final delivery. Its implementation leads to significant improvements in efficiency, cost reduction, and overall productivity, ultimately shaping a more sustainable and competitive manufacturing landscape. This section delves into the profound effects of this technology on various aspects of the manufacturing process.
The integration of sophisticated software solutions transforms traditional manufacturing practices, optimizing workflows and resource allocation. This translates into tangible benefits across the entire production chain, boosting profitability and market competitiveness.
Improved Planning and Scheduling
Manufacturing software provides advanced planning and scheduling capabilities, enabling manufacturers to optimize production schedules based on real-time data and predictive analytics. This leads to reduced lead times, minimized downtime, and improved resource utilization. For instance, a system might analyze historical data, current orders, and machine availability to automatically generate an optimized production schedule, ensuring that the right materials are available at the right time and that machines are used efficiently.
This contrasts sharply with manual planning, which is often prone to errors and delays.
Enhanced Quality Control
Quality control is significantly enhanced through the implementation of manufacturing software. Real-time data monitoring and analysis allow for early detection of defects and deviations from quality standards, leading to immediate corrective actions. Automated inspection systems, integrated with the software, can identify defects with greater accuracy and speed than manual inspections, minimizing waste and improving product quality. Imagine a system that automatically flags a batch of parts that falls outside pre-defined tolerances, alerting the operator before the faulty parts proceed further down the production line.
This proactive approach drastically reduces the risk of shipping defective products.
Streamlined Supply Chain Management and Inventory Control
Efficient supply chain management and inventory control are critical for manufacturing success. Manufacturing software plays a vital role in optimizing these processes by providing real-time visibility into inventory levels, material flows, and supplier performance. This allows manufacturers to accurately forecast demand, optimize inventory levels, and minimize stockouts or overstocking. For example, software can automatically generate purchase orders when inventory levels fall below a certain threshold, ensuring that materials are readily available for production.
Simultaneously, it can track shipments and provide real-time updates on delivery schedules, allowing for proactive management of potential disruptions.
Cost Reduction and Productivity Enhancement
The implementation of manufacturing software translates directly into cost savings and productivity gains. By optimizing resource allocation, reducing waste, and improving efficiency, manufacturers can significantly lower their operational costs. Improved planning and scheduling lead to reduced lead times and minimized downtime, while enhanced quality control reduces waste and rework. The automation of tasks, such as data entry and report generation, frees up employees to focus on more value-added activities, further boosting productivity.
A hypothetical scenario could show a company reducing its production time by 15% and its waste by 10% after implementing a new manufacturing software system, resulting in significant cost savings and increased profits.
Sustainability in Manufacturing
Manufacturing software plays a crucial role in achieving sustainability goals.
Manufacturing software facilitates the implementation of sustainable practices by providing tools for monitoring and optimizing resource consumption, reducing waste, and improving energy efficiency. Here are some specific examples:
- Energy Monitoring and Optimization: Software can monitor energy consumption in real-time, identifying areas for improvement and optimizing energy usage across the manufacturing facility.
- Waste Reduction: By optimizing production processes and minimizing defects, manufacturing software contributes to significant waste reduction, minimizing environmental impact.
- Sustainable Supply Chain Management: Software can track the environmental impact of materials and suppliers, enabling manufacturers to make more informed sourcing decisions and promote sustainable supply chains.
- Carbon Footprint Reduction: Through optimized production processes and reduced waste, the software contributes to a lower carbon footprint for the manufacturing operations.
Future Trends in Manufacturing Software
The manufacturing landscape is undergoing a dramatic transformation, driven by rapid advancements in technology. Software is at the heart of this revolution, enabling unprecedented levels of efficiency, automation, and data-driven decision-making. Understanding the emerging trends in manufacturing software is crucial for businesses seeking to maintain competitiveness and thrive in this dynamic environment.
Emerging Technologies Shaping the Future
Artificial intelligence (AI), the Internet of Things (IoT), and blockchain technology are converging to redefine manufacturing software capabilities. AI-powered predictive maintenance systems, for instance, analyze sensor data from IoT devices to anticipate equipment failures, minimizing downtime and optimizing maintenance schedules. This proactive approach contrasts sharply with traditional reactive maintenance, leading to significant cost savings and increased productivity. Blockchain technology enhances supply chain transparency and traceability, improving security and accountability throughout the manufacturing process.
Imagine tracking a product’s journey from raw material sourcing to final delivery, with every step securely recorded and verifiable on a shared, immutable ledger. This level of visibility fosters trust and enables faster, more efficient responses to disruptions.
Impact on Manufacturing Processes and Business Models
The integration of these technologies is fundamentally altering manufacturing processes and business models. AI-driven automation is increasing efficiency and reducing labor costs, while IoT-enabled data collection provides real-time insights into operational performance. This data-driven approach allows manufacturers to optimize production schedules, improve quality control, and personalize products to meet specific customer needs. Furthermore, blockchain technology is fostering greater collaboration and transparency within supply chains, creating more resilient and efficient networks.
Companies like Walmart are already leveraging blockchain to track food products, ensuring safety and preventing contamination. This enhanced transparency builds trust with consumers and strengthens brand reputation.
Predictions for the Future Evolution of Manufacturing Software
We can expect to see a continued convergence of AI, IoT, and blockchain within manufacturing software. This will lead to the development of more intelligent, autonomous, and secure systems. The user interface will become increasingly intuitive and user-friendly, leveraging augmented reality (AR) and virtual reality (VR) to provide immersive experiences for operators and engineers. Predictive analytics will become even more sophisticated, enabling manufacturers to anticipate and respond to market changes more effectively.
The rise of digital twins – virtual representations of physical assets – will facilitate advanced simulation and optimization, enabling manufacturers to test and refine processes before implementation.
Hypothetical Advanced Manufacturing Software Solution
Imagine a software solution called “Synapse Manufacturing,” a comprehensive platform integrating AI, IoT, and blockchain. Its user interface is a sleek, intuitive dashboard displaying real-time data visualizations from connected machines and sensors across the entire production line. AR overlays provide operators with step-by-step instructions and real-time performance metrics. AI-powered algorithms analyze this data to predict potential problems, optimize resource allocation, and automate routine tasks.
Blockchain technology ensures secure and transparent tracking of materials and products throughout the supply chain, from origin to consumer. Synapse Manufacturing would also incorporate advanced simulation capabilities, enabling users to test different scenarios and optimize processes before implementation. The system’s self-learning capabilities would constantly improve its performance and adapt to changing conditions, ensuring maximum efficiency and profitability.